Prod Model: |
BLADE MODEL SY-DSB-78 |
Markets: |
North America,South America,Eastern Europe,Southeast Asia,Africa,Oceania,Mid East,Eastern Asia,Western Europe |
Welding: |
Laser Weled |
Inner Hole: |
16mm 22.23mm 25.4mm 50mm 60mm |
Painting: |
as Customers' Request |
ODM: |
Acceptable |
Certification: |
BV/SGS/ISO |
Delivery Time: |
7 - 15 Days |
Graininess: |
300# |
Kind: |
Diamond Saw Blade |
Manufacturing Arts: |
Laser Welded |
Usage: |
Concrete, Green Concrete, Reinforced Concrete |
Product Description
Diamond Saw Blade Cutting ConcreteDesign the segment bond according to your different materials' hardness, abrasiveness, machine, parameter to bring premium cutting and maximum output.
Features: 1. laser welding concrete saw blade are mainly applied to cutting concrete, hard concrete, hard concrete with reinforced bar, block, brick, hard brick, pavers, clay pavers and field stones.
2. laser welded segment can increase strength under high temperature and provid better cutting performance .
3. Faster cutting and longer service life, includes "drop segments" to protect the blade core from abrasive material erosion. 
BASIC INFO |
Brand | SUNNY |
Product Name | Diamond Saw Blade Cutting Concrete |
Item No. | SY-DSB-1001 |
Diameter
| 300mm---800mm |
Material | Diamond |
Origin | Quanzhou, Fujian, China |
Application | Used for Concrete, Asphalt, Brick etc cutting |
Laser welding concrete saw bladeDiameter | Bore | Blade thickness | Seg height (mm) |
12"(300mm) | 50/25.4mm | 2.2mm | 10/12mm |
14"(350mm) | 50/25.4mm | 2.2mm | 10/12mm |
16"(400mm) | 50/25.4mm | 2.6mm | 10/12 |
18"(450mm) | 50/25.4mm | 2.8mm | 10/12mm |
20"(500mm) | 50/25.4 | 3.2 | 10/12 |
24"(600mm) | 50/25.4 | 3.2 | 10/12 |
26"(650mm) | 50/25.4mm | 3.6 | 10/12 |
30"(750mm) | 50/25.4mm | 4 | 10/12 |
32"(800mm) | 50/25.4mm | 4 | 10/12 |
36"(900mm) | 50/25.4mm | 5.2 | 10/12 |
Wall Saw BladeDiameter(mm) | Bore(mm) | Blade thickness(mm) | Seg height (mm) |
20"(500mm) | 60/25.4 | 3.2 | 10/12 |
24"(600mm) | 60/25.4 | 3.2 | 10/12 |
28"(700mm) | 60/25.4 | 3.6 | 10/12 |
32"(800mm) | 60/25.4 | 4.5 | 10/12 |
36"(900mm) | 60/25.4 | 5 | 10/12 |
40"(1000mm) | 60/25.4 | 5 | 10/12 |
48"(1200mm) | 60/25.4 | 5.5 | 10/12 |
Tuck point bladeDiameter(mm) | Bore(mm) | Seg height (mm) | Application |
4"(105) | 50/25.4 | 8/10 | stone, concrete, asphalt, fire brick |
4.5"(115) | 50/25.4 | 8/10 |
5"(125) | 50/25.4 | 8/10 |
6"(150) | 50/25.4 | 8/10 |
7"(180) | 50/25.4 | 8/10 |
8"(200) | 50/25.4 | 8/10 |
9"(230) | 50/25.4 | 8/10 |
Ring Saw BladeDiameter(mm) | Bore(mm) | Seg height (mm) |
14"(350mm) | 366×4.2×288 | 8/10 |
16"(400mm) | 406×3.9×326.78 | 8/10 |
20"(500mm) | 506×3.9×421.78 | 8/10 |
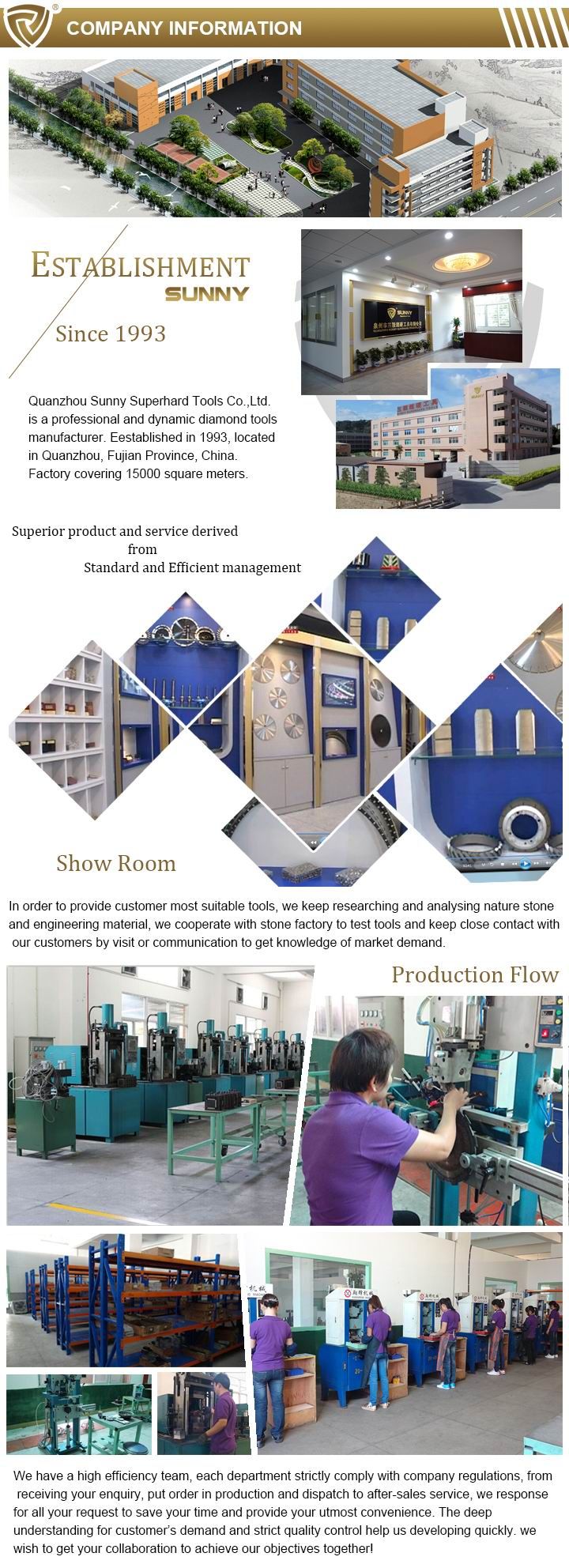
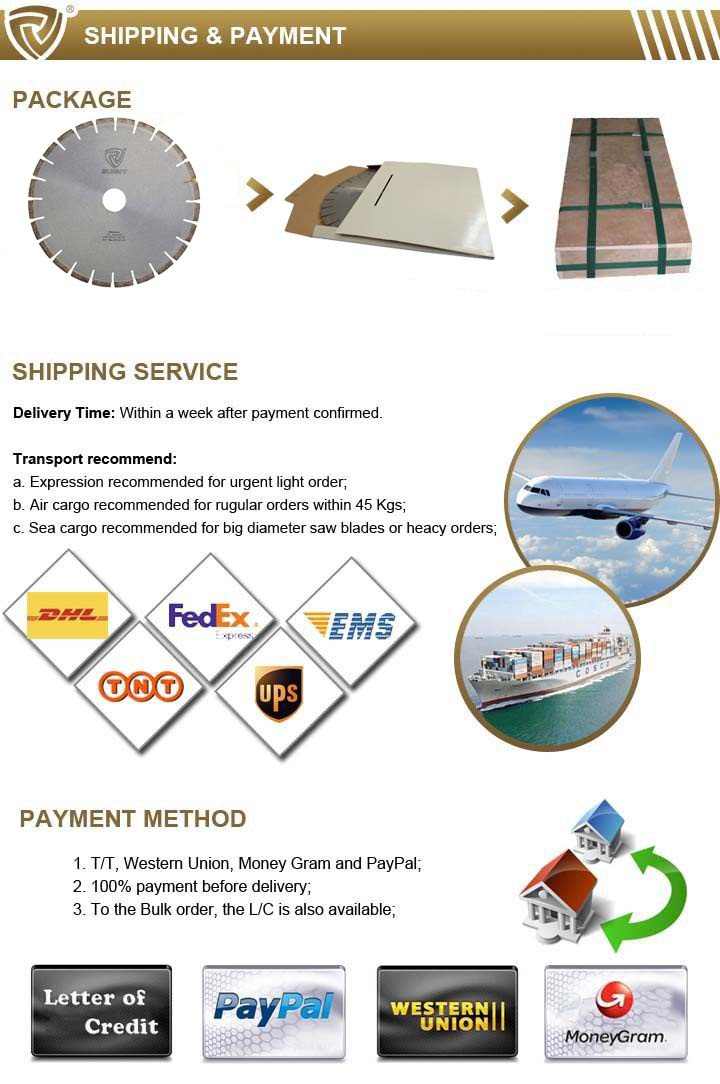
Concrete Diamond Blade-FAQ and Troubleshooting.
Sunny has prepared this guide to help you find, identify and resolve the problems which you may encounter with diamond saw blades.
The majority of problems encountered arise from:
- the use of a blade not suited to the job,
- the incorrect use of a blade,
- equipment faults.
Click a symptom below to see its cause and remedyLoss of tensionSymptom | Cause | Remedy |
There is "undercutting" when the steel plate wears more rapidly than the diamond segment, particularly at the joint between the segments and the steel plate. | The blade is being used on a poorly aligned saw. | Correct the alignment of the saw. | The blade is too hard in relation to the material being cut, which causes excessive stress on the steel plate. | Ensure that the blade is suitable for the material being cut (consult the selection table or see your distributor). | Slippage of the material causes deformation of the blade which twists or bends. | Hold the material firmly while sawing. | The use of flanges which are too small or not of the same diameter causes unequal pressure on the steel plate. | Ensure that the flanges are of the right size and the same diameter. | The blade is poorly fitted onto the spindle and bends when the flanges are tightened. | Hold the blade on the spindle until the outer flange and the nut have been firmly tightened. | The blade is being used at the wrong speed of rotation. | Check whether the spindle is rotating at the correct speed, using a tachometer. This precaution is particularly important for concrete saws. | The steel plate heats up due to friction caused by too rapid or uneven wear of the rim. | Use a blade with more side clearance or of a specification more suited to the material. |
|
UndercuttingSymptom | Cause | Remedy |
| This situation is caused by grinding of the blade by very abrasive materials during sawing. Usually materials with a high sand content are responsible for this type of wear (see section "Loss of segment"). | The abrasive slurry must be dispersed over a greater area, away from the critical zone of the segment. Very often, it is sufficient to use protective segments placed on the steel plate to modify the areas constantly subject to abrasion. Although they are effective in the majority of cases, these segments do not give total protection. Use a high flow of water to remove the slurry. | With a floor saw, when cutting in one pass through more than the total thickness of the material, the cooling water escapes from the cutting line and this causes the blade to overheat. | Adjust the depth of cut so that a few millimetres of uncut material remains; this will hold the cooling water in the kerf. |
|
Uneven segment wearSymptom | Cause | Remedy |
| The segments are worn on one side only, which reduces the side clearance. This wear is generally caused by poor blade alignment or inadequate cooling on both sides of the blade. | Check the saw alignment. Clean the cooling device, ensure that the front edge of the flange is correctly cooled. Check that the pump is supplying water in sufficient quantities and regularly. (See section "Excessive wear" below). | The blade has lost its circular shape because of wear caused by poor bearings, a worn spindle, dirty or damaged flanges or even excessive baulking. (See section "Excessive wear" below). | Replace the bearings or the worn spindle as necessary; do not remove the drive pivot pins when supplied with the flanges. |
|
Excessive WearSymptom | Cause | Remedy |
| The blade used is not suitable for the highly abrasive material being cut (e.g: a tile-cutting blade used on a concrete block). | See the blade selection table or consult your distributor who will indicate the correct blade specification. | Blade cooling is insufficient; this problem is often found because of excessive wear in the centre of the segment. (Note: in the two cases mentioned above, the diamonds generally project very sharply). | Clean the cooling system. Ensure that the water pump is operating correctly. | Wear accelerates if the blade has lost its circular shape; this may be due to poor bearings, a worn spindle or the use of a blade which is too hard in relation to the material being cut. | Check the bearings and the spindle. If they are worn, replace them before fitting a new blade. | Output power is insufficient because V-belts are not properly tensioned, voltage is inadequate or speed is incorrect. | Tension the belts correctly. Replace worn belts. Check the voltage. Use an appropriate power source. | Cutting speed is too fast. | Reduce the speed of advance. | Blade is not perpendicular to the material being cut. | Check the speed of the blade's drive spindle and the flanges to ensure correct alignment of the blade and of the machine. | Spindle is rotating too slowly. | Check the speed of the drive spindle. If necessary, change the equipment or modify speed of rotation. |
|
Cracked centre plateSymptom | Cause | Remedy |
| The blade is too hard for the material being cut. | Use the appropriate blade with a softer bond. | Cutting pressure is too high or a blade jammed or twisted in the cut may bend or flex the blade's steel plate. When it is subjected to extreme tension and to metal fatigue, there is a risk of the steel plate cracking. | The operator must use stable, even pressure to make the tool penetrate the material and should take care not to twist or jam the blade in the cut. | A cracked centre can be a consequence of overheating. Overheating is caused by inadequate water supply or incorrect use of a blade intended for dry cutting. | Use sufficient water to cool diamond blades for wet cutting (e.g. 7-18 litres / minute for floor saws). Allow sufficient air to circulate around the diamond blades when dry cutting so as to prevent overheating. | Excessive speed of rotation. | Check the machine's speed of rotation; if necessary, change the equipment or blade. |
|
Loss of blade segmentsymptom | cause | remedy |
Does a blade need repairing? It is possible to replace two or three missing diamond segments providing the plate is not cracked or badly worn. If numerous segments are missing or if only 50% of the practical life of the blade remains, it may not be worthwhile repairing the diamond blade. Ensure there is no other mechanical or operational problem before replacing the blade. | The material slips during cutting, which twists or jams the segments enough to break them. | Secure the material firmly while cutting. | The blade is too hard for the material being cut, which causes excessive polishing, which breaks off the segment or causes fatigue. | Use a blade with a softer bond. Consult the blade specification tables. | When worn, the flanges do not provide the necessary support, which causes the blade to deviate. | Replace the two flanges. | The rotation of an ovalised blade (because of a worn spindle or poor bearings) causes the segments to break. | Replace the worn spindle and/or bearings. | Loss of segment caused by overheating. Overheating is detectable by the steel plate taking on a bluish colour, generally limited to where the segment is missing. | Check that the cooling system is not blocked. Test the pump. In the case of dry cutting, it may be necessary to reduce the depth of cut and, after a few minutes, allow the blade to turn freely and cool in the air. | The segment has suffered knocks when moving the machine or when in contact with the material. | Avoid knocking the blade during transport; bring the blade gently into contact with the material. |
|
Cracked segmentSymptom | Cause | Remedy |
| The blade is too hard for the material being cut. | Use a blade with a softer bond.Adjust cutting speed. | Cutting speed is too fast. | Reduce the speed of advance. |
|
EccentricitySymptom | Cause | Remedy |
| The bond is too hard for the material being cut. A hard bond retains the diamonds which start to round off, thereby smoothing the blade. Instead of cutting, the blade starts to hammer and thereby loses its circular shape. | Use a softer bond that will wear away more easily, allowing the smooth diamonds to become detached and new sharp edges to surface. | If the spindle bearings are worn, the spindle and the mandrel will rotate eccentrically, which will cause the blade to lose its circular shape. This problem occurs most often with concrete saws when the necessary lubrication of the bearings is neglected. | Fit new bearings. In some cases, it may be necessary to replace the spindle as well if it is worn or if it is no longer properly aligned. |
|
Overheated bladeSymptom | Cause | Remedy |
| The necessary cooling water has not been adequately distributed. | Check that the volume of water is sufficient and that the cooling system is not blocked. Use dry blades for shallow cuts only (2 to 5 cm deep) or for cutting with several passes. Let the blade turn freely every 10 to 15 seconds to allow the air to cool it. | Incorrect specification for the material to be cut. | Consult the blade selection table for the appropriate specification. | Cutting speed is too fast. | Reduce the speed of advance. |
|
Ovalised bore holeSymptom | Cause | Remedy |
If the oval shape is not too exaggerated, return the blade to the factory for possible repairs. | The spindle is badly worn because the blade is poorly fitted. | Check that the blade is properly fitted on the spindle before tightening the flanges. | If the flanges are not tightened, the blade will rotate around the spindle. | Always tighten the nut on the spindle with a spanner; do not just tighten it by hand. Always use hexagonal nuts and never wing nuts. | The flanges or the spindle are worn and do not provide the blade with the necessary support. | Check the wear on the flanges and spindle. The wear on the two flanges must not be greater than that recommended by the manufacturer. Replace worn parts. |
|
The blade will not cutSymptom | Cause | Remedy |
| The blade is too hard for the material being cut (e.g. a blade for a block or a universal blade used for a prolonged period on hard brick; a blade for asphalt used to cut reinforced concrete). | See the blade selection table or consult your distributor or the manufacturer who will indicate the proper blade for the material to be cut. | The output power is inadequate to allow the blade to cut correctly (belts too slack, voltage and motor output insufficient). | Check the belts, the voltage and the motor output power. | The blade segments still appear to have some life left but the blade is not cutting. | Cut an abrasive material until the diamonds surface again. This remedy may prove necessary from time to time; however, if the blade becomes dull too often, this probably means it is too hard for the material being cut. | The blade segments still appear to have some life left but the blade is not cutting. | The segments of a blade with a harder bond provided for abrasive materials require a non-diamond support at the base of the diamond segment in order to achieve better adherence to the steel plate. Wearing of the blade to this state is considered normal wear. The blade must therefore be replaced. | The tool becomes smooth because of excessive speed of rotation. | Match the specification and the diameter of the blade to the machine. | The tool becomes smooth due to excessive pressure of the blade on the material to be cut. | Ensure that the pressure of the blade on the material allows natural sharpening of the blade without any excess. |
|
Advantage:WHY CHOOSE US?
1. More than 22 years experience in diamnd tools;
2. Get knowledge of market demand;
3. 12 experienced professors and engineers;
4. High efficiency production flow;
5. Strict quality control system;
6. Exported to more than 60 countries;
7. Professional sales team with prompt reply;
Contact us:Quanzhou Sunny Superhard Tools Co., Ltd.
Add: Tangxi Industrial Zone, Luojiang, Quanzhou, Fujian, China
Postcode:362010
TEL: 86 - 595 - 22003682
FAX: 86 - 595 - 22003987
Web: http://www.sunnytools.biz
http://www.concretetoolsunny.com
QUANZHOU SUNNY SUPERHARD TOOLS Co., Ltd is a professional and Dynamic Diamond Tools manufacturer, established in 1993, Located in Quanzhou, Fujian province, China, factory covering 15000 square meters. Our technical department is composed of experienced professors and engineers. We devote ourselves to researching and manufacturing cutting and processing Diamond tools for nature stone and building materials. Our tools are exported to more than 60 countries, including America, Brazil, Italy, Russia, Ukraine, India, Egypt, South Africa etc.
Main Products:
Cutting Tools (Saw blade, Segment, Wire saw etc)
Grinding&Polishing Tools (Calibration Rollers, Fickerts, Frankfurt, Cup wheel, Profilling wheel, Polishing pad, brush etc)
Drilling Tools (Finger Bit, Core drill etc)
The Philosophy of Sunny is "Superior product and service derived from standard and efficWe have a high efficiency team, each department strictly comply with company regulations.
From receiving your enquiry, put order in production and Dispatch to after-sales service, Ient management. "
In order to provide customer most suitable tools, we keep researching and analysing nature stone and engineering material. We cooperate with stone factory to test tools, and keep close contact with our customers by visit or communication to get knowledge of market demand.
We Response All Your Request efficiently To Save Your Time And Provide Your Utmost Convenience.
The deep understanding for customer's demand and strict quality control help us developing quickly, we wish to get your collaboration to achieve our objectives together!
Our aim is to provide our clients stable and consistant quality with competitive price.
Advantages enable clients benefits from our tools.
1. Experienced bond system
2. Advanced equipment and high grade raw material
3. Strictly production procedures control and quality inspection.
4. Customer's active feedback and support help us developing fast.